رنگنے کی مسلسل مشین ایک بڑے پیمانے پر پیداواری مشین ہے اور اس کے لئے پیداوار کے دوران استعمال ہونے والے سلیکون آئل کی استحکام کی ضرورت ہوتی ہے۔ کچھ فیکٹریوں کو ٹھنڈک کے ڈھول سے لیس نہیں کیا جاتا ہے جب اس کے نیچے مسلسل رنگنے والی مشین کو خشک کرتے ہیں ، لہذا تانے بانے کی سطح کا درجہ حرارت بہت زیادہ ہوتا ہے اور ٹھنڈا کرنا آسان نہیں ہوتا ہے ، استعمال شدہ سلیکون آئل میں درجہ حرارت کی مزاحمت ہونی چاہئے۔ ایک ہی وقت میں ، اس کے رنگنے کے عمل سے رنگین رکاوٹ پیدا ہوگی اور اس کی مرمت کرنا مشکل ہے۔ چونکہ رنگین رنگت کی مرمت کے لئے رنگنے سے رولنگ بیرل میں ایک سفید فام ایجنٹ شامل ہوجائے گا ، جس میں سلیکون آئل کو رنگنے اور سفید کرنے والے ایجنٹ سے ملنے کے لئے درکار ہوتا ہے اور کوئی کیمیائی رد عمل نہیں ہوتا ہے۔ تو رنگنے کے مسلسل عمل میں کون سا رنگین رکاوٹ واقع ہوتی ہے؟ اور اسے کیسے کنٹرول کیا جاسکتا ہے؟ کس طرح کا سلیکون تیل اسے حل کرسکتا ہے؟
کپاس لمبی کار رنگنے سے پیدا ہونے والی رنگین قسم کی قسم
روئی کے مسلسل رنگنے کے عمل کی آؤٹ پٹ میں رنگین رکاوٹ عام طور پر چار قسموں پر مشتمل ہوتی ہے: اصل نمونے کی رنگین خرابی ، اس سے پہلے اور اس کے بعد رنگین رکاوٹ ، بائیں بازو کے دائیں رنگ کے رنگین مسخ ، اور فرنٹ اینڈ بیک کرومیٹک خرابی۔
1. اصل نمونے کی رنگین خرابی سے مراد رنگین تانے بانے اور کسٹمر کے آنے والے نمونے یا معیاری رنگ کارڈ کے نمونے کے درمیان رنگ کی رنگت اور رنگ کی گہرائی سے مراد ہے۔
2. اس سے پہلے اور اس کے بعد رنگین خراش اسی سایہ کے یکے بعد دیگرے رنگے ہوئے کپڑے کے درمیان سایہ اور گہرائی میں فرق ہے۔
3. بائیں ، دائیں رنگ کے رنگ کے رنگ کے بائیں ، مرکز ، یا تانے بانے کے دائیں حصے میں رنگین کی گہرائی اور رنگ کی گہرائی سے مراد ہے۔
4. سامنے اور پیچھے رنگنے والی رنگت سے مراد رنگ کے مرحلے کی تضاد اور تانے بانے کے سامنے اور پچھلے اطراف کے درمیان رنگ کی گہرائی سے مراد ہے۔
رنگنے کے عمل میں رنگین رکاوٹیں پری پیڈ اور کنٹرول کیسے کی جاتی ہیں؟

اصل نمونوں میں رنگین رکاوٹ بنیادی طور پر رنگ ملاپ کے لئے ڈائیسٹف کے غیر معقول انتخاب کی وجہ سے ہوتی ہے اور مشین رنگنے کے دوران نسخے کی غلط ایڈجسٹمنٹ۔ چھوٹے نمونے کی نقل کرتے وقت رنگین مسدود کرنے کے لئے ڈائیسٹف کے غیر معقول انتخاب کو روکنے کے لئے درج ذیل احتیاطی تدابیر اختیار کی گئیں۔
نسخے میں رنگوں کی تعداد کو کم سے کم رکھا جانا چاہئے ، کیونکہ مختلف رنگوں میں رنگنے کی مختلف خصوصیات ہیں ، اور رنگوں کی تعداد کو کم کرنے سے رنگوں کے مابین مداخلت کو کم کیا جاسکتا ہے۔
نسخے میں ، رنگنے اور ملاوٹ کا استعمال کرنے کی کوشش کریں جو اصل نمونے کے قریب ہے۔
اسی طرح کی رنگنے والی خصوصیات کے ساتھ رنگ استعمال کرنے کی کوشش کریں۔
پالئیےسٹر اور روئی کے مابین دو مرحلے کی گہرائی کا انتخاب: جب ہلکے رنگوں کو رنگنے کے وقت ، پالئیےسٹر کی گہرائی قدرے ہلکا ہونی چاہئے اور روئی کی گہرائی قدرے گہری ہونی چاہئے۔ جب سیاہ رنگوں کو رنگنے کے وقت ، پالئیےسٹر کی گہرائی قدرے گہری ہونی چاہئے ، جبکہ روئی کی گہرائی قدرے ہلکا ہونی چاہئے۔
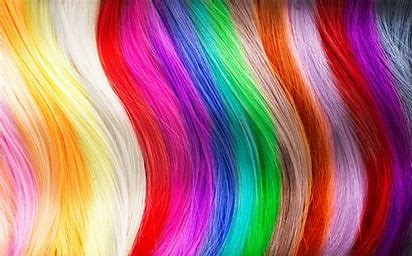

فائننگ میں ، تانے بانے کا پہلے اور بعد کے رنگین رکاوٹ بنیادی طور پر چار پہلوؤں کی وجہ سے ہوتا ہے: کیمیائی مواد ، مشینری اور سازوسامان کی کارکردگی ، نیم مصنوعات کا معیار ، عمل پیرامیٹرز اور حالات میں تبدیلی۔
ایک ہی سایہ کے رنگنے والے کپڑے ایک ہی پری علاج کے عمل کا استعمال کرتے ہوئے۔ جب ہلکے رنگوں کو رنگنے کے وقت ، یہ ضروری ہے کہ مستقل سفیدی کے ساتھ بھوری رنگ کے تانے بانے کا انتخاب کریں ، کیوں کہ اکثر بھوری رنگ کے تانے بانے کی سفیدی رنگنے کے بعد رنگین روشنی کا تعین کرتی ہے ، اور جب منتشر/رد عمل رنگنے کے عمل کا استعمال کرتے ہیں تو ، یہ خاص طور پر اہم ہے کہ پییچ ویلیو فیبرک کے ہر بیچ سے مطابقت رکھتی ہے۔ اس کی وجہ یہ ہے کہ جب رنگوں کے جوڑے ہوتے ہیں تو بھوری رنگ کے تانے بانے کے پییچ میں ہونے والی تبدیلیوں سے پییچ کی تبدیلیوں پر اثر پڑے گا ، جس کے نتیجے میں تانے بانے میں پہلے اور بعد میں رنگین رکاوٹ پیدا ہوجاتی ہے۔ لہذا ، تانے بانے کے پہلے اور بعد کے رنگین گھماؤ کی مستقل مزاجی کو صرف اس صورت میں یقینی بنایا جاتا ہے جب رنگنے سے پہلے بھوری رنگ کے تانے بانے اس کی سفیدی ، مجموعی کارکردگی اور پییچ ویلیو میں مطابقت رکھتے ہوں۔
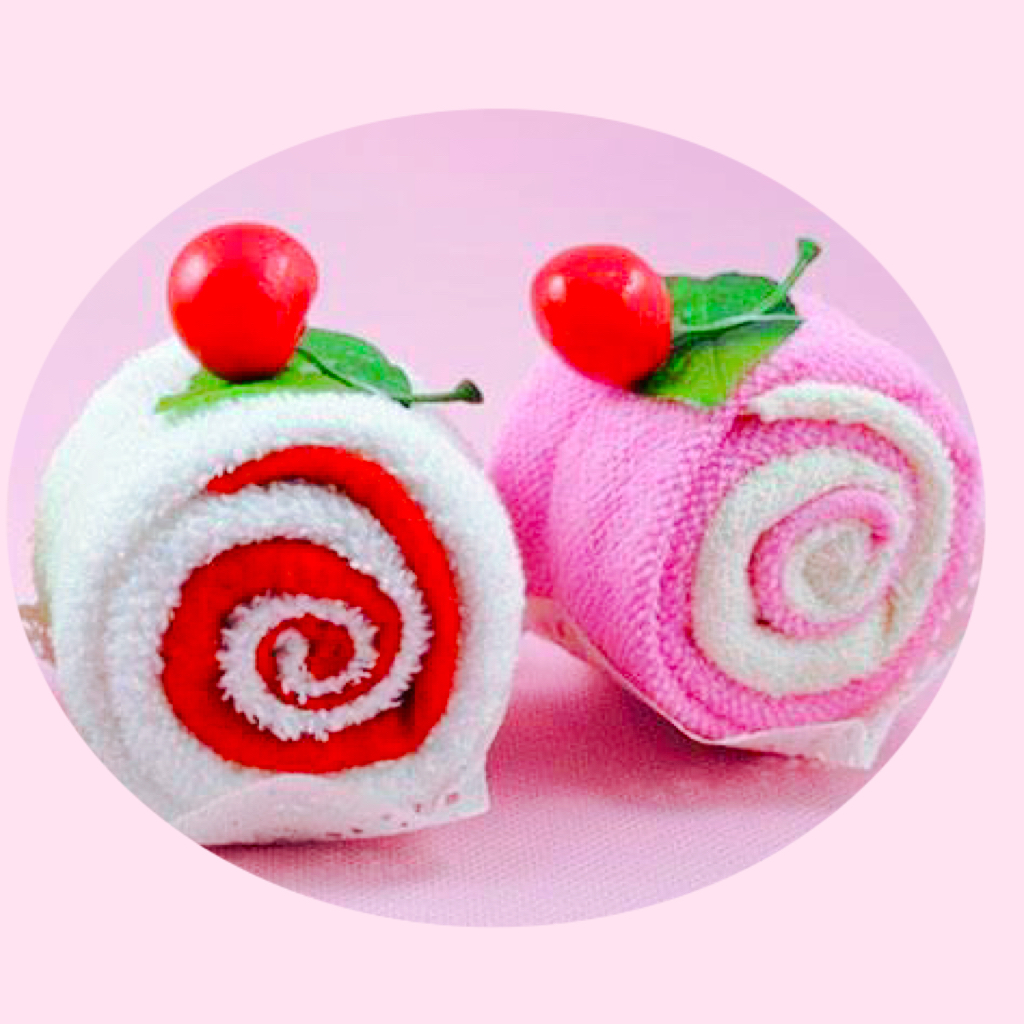

رنگنے کے مستقل عمل میں بائیں بازو کے دائیں رنگ کا فرق بنیادی طور پر رول پریشر اور گرمی کے علاج دونوں کی وجہ سے ہوتا ہے جس میں تانے بانے کا نشانہ بنایا جاتا ہے۔
رولنگ اسٹاک کے بائیں طرف اور دائیں طرف کا دباؤ اسی طرح رکھیں۔ رنگنے کے حل میں تانے بانے کو ڈوبنے اور لپیٹنے کے بعد ، اگر رول پریشر مستقل نہیں ہے تو ، اس سے مائع کی غیر مساوی مقدار کے ساتھ تانے بانے کے بائیں ، مرکز اور دائیں اطراف کے درمیان گہرائی میں فرق پیدا ہوگا۔
جب رولنگ ڈسپلے رنگ جیسے بائیں درمیانی دائیں رنگ کے فرق کے ظہور کو وقت کے ساتھ ایڈجسٹ کیا جانا چاہئے ، کبھی بھی دوسرے رنگوں کے سیٹ میں ایڈجسٹ کرنے کے لئے سیٹ نہ کریں ، تاکہ تانے بانے کا بائیں وسط دائیں فرق کے رنگ مرحلے میں ظاہر ہوجائے ، اس کی وجہ یہ ہے کہ پالئیےسٹر اور روئی کا رنگ کا مرحلہ مکمل طور پر مستقل نہیں ہوسکتا ہے۔
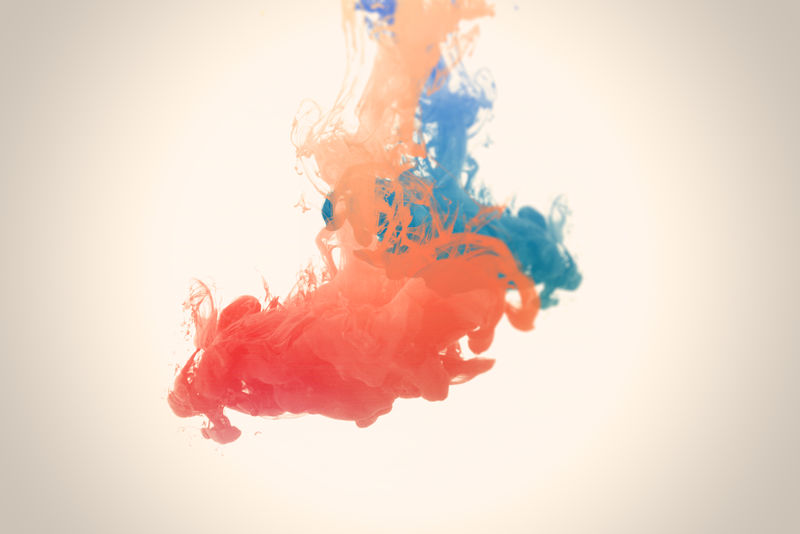

پالئیےسٹر کپٹن ملاوٹ والے کپڑے کی مسلسل رنگنے اور تکمیل میں ، تانے بانے کے سامنے اور پچھلے حصے کے درمیان رنگ میں فرق بنیادی طور پر تانے بانے کے سامنے اور پچھلے حصے میں متضاد گرمی کی وجہ سے ہوتا ہے۔
تانے بانے ڈپ رنگنے والے مائع اور گرم پگھل فکسنگ کے خشک ہونے والے عمل میں ، یہ ممکن ہے کہ سامنے اور پیچھے رنگین گھماؤ پیدا کیا جاسکے۔ سامنے کی طرف کی رنگین خرابی رنگ میں ہجرت کی وجہ سے ہے۔ ڈائی کے گرم پگھلنے کے حالات میں تبدیلی کی وجہ سے پچھلے حصے کی رنگین رکاوٹ ہے۔ لہذا ، مندرجہ بالا دو پہلوؤں سے فرنٹ اینڈ بیک بیک رنگی خراش کو کنٹرول کرنے کے لئے غور کیا جاسکتا ہے۔
پوسٹ ٹائم: فروری 25-2022